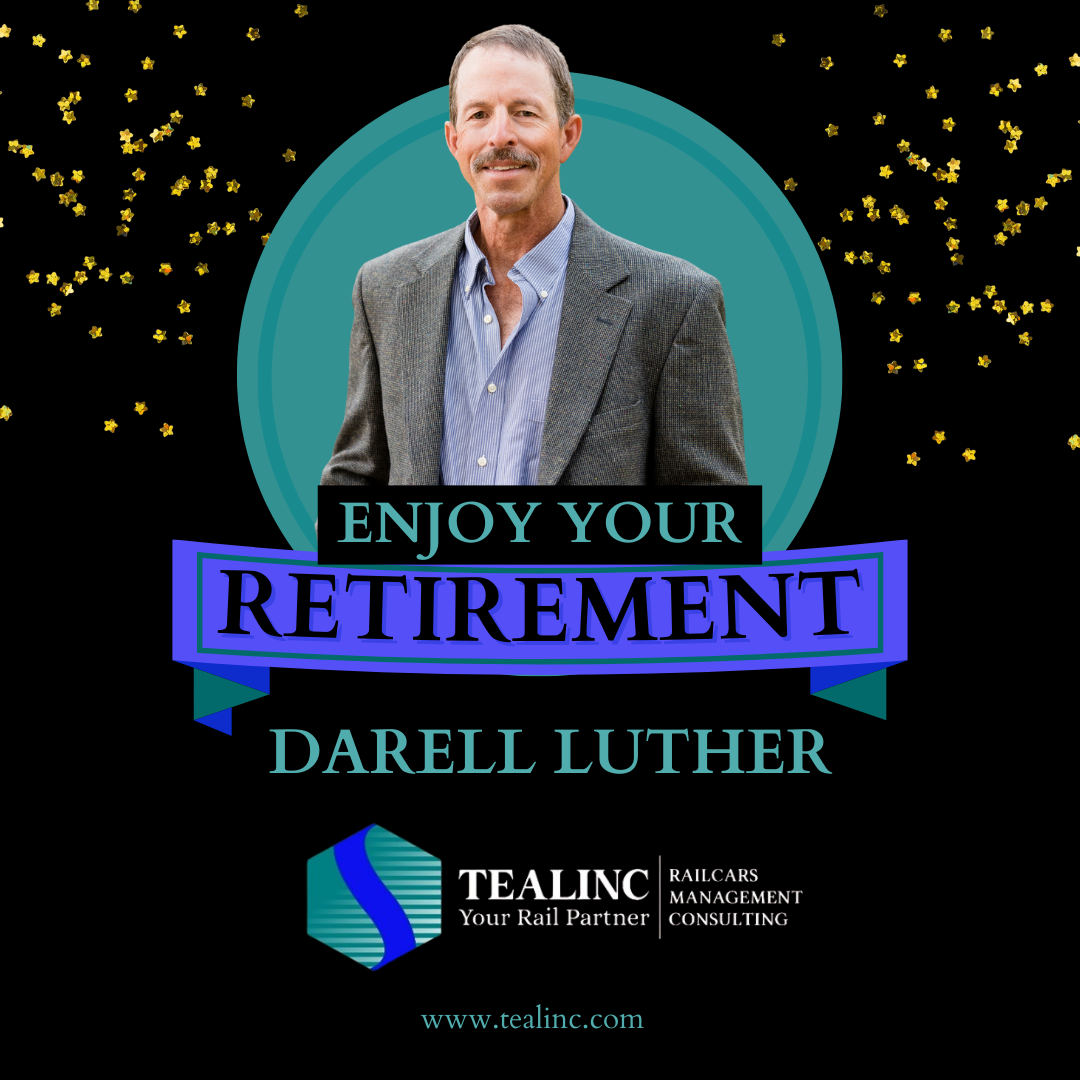
Tealinc Announces the Retirement of CEO and Founder Darell Luther
FOR IMMEDIATE RELEASE
April 1, 2025
Forsyth, MT – Tealinc LLC, a premier railcar leasing company specializing in railcar asset ownership, leasing, and rail fleet management services, announces the retirement of its CEO and Founder, Darell Luther, effective April 1, 2025.
After 38 remarkable years in the rail industry, Darell Luther is stepping down leaving behind a legacy defined by strategic foresight and an unwavering dedication to excellence. Under his guidance, Tealinc has become widely recognized for its tailored rail transportation solutions, exceptional railcar leasing capabilities, and unparalleled depth of industry knowledge.
“Darell didn’t just build a company, he created a lasting legacy driven by integrity, remarkable creativity, and an extraordinary ability to deliver solutions that consistently provided outstanding customer value” said President Julie Mink. “We are excited to celebrate Darell’s profound contributions and wish him happiness in his retirement. Our team remains committed to building upon Darell’s visionary foundation, ensuring his impact in the rail industry continues in our work for many years to come.”
Darell will remain on the Board of Directors to Tealinc and will continue to work closely with Julie Mink, President of Tealinc since 2015, who will continue to lead the company through Darell’s transition. Please join us in celebrating Darell’s remarkable career and contributions to the rail industry. Messages of appreciation can be shared with him at darell@tealinc.com or on his LinkedIn Profile.
About Tealinc LLC
Tealinc LLC is a premier rail transportation solutions provider specializing in railcar asset ownership and leasing, rail fleet management and support services. Our wide range of services includes railcar leasing and sales, railcar purchasing, railcar fleet management, rail transportation consulting and strategic development. Our customized solutions are tailored to meet the specific needs of each of our customers, and our flexible leasing options allow for maximum flexibility and cost-effectiveness. We’re dedicated to providing personalized and innovative rail transportation services to our customers.
Darell Luther’s Career Highlights
Tealinc, Ltd. & Tealinc LLC (2002 – Present)
Founder and CEO, providing railcar leasing, asset management, consulting, and logistics solutions. Darell’s leadership drove Tealinc to industry prominence, significantly enhancing customer transportation efficiencies.
DTE Rail Services, Inc. & DTE Transportation Services, Inc. (1998 – 2002)
As President, Darell led rapid financial and operational growth through railcar repair solutions, shipment management, leasing, fleet sizing, and railcar trading, achieving significant profitability improvements.
Fieldston Transportation Services, LLC (1996 – 1998)
President and co-founder, Darell specialized in strategic bulk commodity transportation management, fleet planning, logistics, and cost-saving solutions for clients.
Southern Pacific Railroad (1992 – 1995)
Managing Director of Coal and Unit Trains and Managing Director of Hoppers and Copper, overseeing extensive operations and budgeting for thousands of railcars and unit trains.
Burlington Northern Railroad (1991 – 1992)
Instrumental in fleet management, logistics, strategic planning, and business integration, significantly contributing to operational efficiencies.
Education
• M.S., Business Management – University of Mary, Bismarck, ND (1987)
• B.S., Agricultural Education – Montana State University, Bozeman, MT (1984)
Industry Leadership
Darell has served as a recognized thought leader, contributing through keynote speeches, advisory board roles, and published articles in industry publications. His insights have significantly shaped rail transportation management and logistics.
For more information, visit www.tealinc.com.
Related industry article: Pit and Quarry
Tealinc Featured in Coal Age!
Tealinc CEO Darell J. Luther was recently featured in Coal Age, discussing the rapid decline of the coal railcar fleet—down 29% since 2013—and what it means for the industry. As data centers and other factors influence future coal demand, railcar availability could become a major challenge.
Read the full article to see how these shifts impact coal logistics and how Tealinc helps businesses navigate evolving transportation needs.
📖 Read More: Coal Age Feature
📖 Flipbook Version: January/February Issue
Let us help you optimize your railcar strategy—contact us today!
Tealinc Celebrates 1st Anniversary Under New Ownership!
FOR IMMEDIATE RELEASE
Date: November 20, 2024
Tealinc Celebrates 1st Anniversary Under New Ownership!
Tealinc LLC, a provider of railcar equipment leasing, sales, and fleet management solutions, is thrilled to announce the one-year anniversary of its acquisition by a private, family-owned premium finance firm. Although the transaction details were not made public, this marks the first public announcement of the company’s ownership change.
The recent ownership transition has infused Tealinc with increased capital, allowing Tealinc to acquire railcars in even larger volumes, providing railcar shippers with streamlined and competitive options for selling, leasing, buying, and managing their railcar equipment assets.
Reflecting on the last twelve months, Tealinc President Julie Mink stated, “This past year has been a transformative period of growth and refinement. With the infusion of capital from our new owners, we’re leveraging our teams combined knowledge of over 115-years of rail industry experience and expanding our railcar fleet. We’re focused on delivering even greater flexibility and enhanced value to railcar sellers and railcar leasing customers alike. We’re excited to build on this momentum and to create successful synergies with rail industry partners in the years ahead!”
Expanded Resources and New Team Talent
In January 2024, Tealinc proudly welcomed Nate Chilton as the new Director of Railcar Leasing & Sales. Bringing extensive experience in the rail industry, Mr. Chilton joins Tealinc’s leadership team, which includes CEO Darell Luther, President Julie Mink, and Directors Shannon Rodgers and Yvonne Lufborough. Together, this dedicated team is committed to enhancing Tealinc’s services in railcar leasing, purchasing, selling, and fleet optimization.
Looking forward, Tealinc aims to deepen its collaborations within the rail industry, expand its railcar fleet, and continue enhancing its customer-focused solutions. The company remains committed to providing unparalleled service to railcar owners, railcar leasing customers, and rail fleet management partners while strengthening its industry impact.
About Tealinc LLC
Founded by Darell Luther in 2002, Tealinc LLC is a railcar leasing, sales, and rail fleet management services company, dedicated to helping customers optimize their railcar needs with customized rail transportation solutions. The company’s expertise extends across various industries, including agriculture, energy, recycling, manufacturing, and more.
Tealinc LLC – Moving Forward with Excellence!
For further information, please contact:
Julie Mink, President Tealinc LLC | www.tealinc.com | julie@tealinc.com
Office: (720) 733-9922 | Mobile: (720) 384-6385
Nate Chilton Joins Tealinc LLC!
Press Release…
Tealinc LLC (“Tealinc”), a freight railcar owner, lessor, and rail transportation solutions company, is proud to announce that Nathan “Nate” Chilton has been appointed Director: Railcar Leasing & Sales. Nate will be based in the Tealinc – Broomfield, CO office.
As a seasoned professional with a proven track record in the railcar industry, Nate brings a wealth of knowledge, experience, and a fresh perspective to Tealinc. Known for his high-energy, enthusiasm, and visionary approach to the rail industry, Nate is set to elevate Tealinc’s railcar lease, purchase, and sales strategies. In conjunction with Tealinc’s revitalized business plan and increased railcar acquisition initiatives, Nate is poised to support Tealinc long-term growth model.
“We are thrilled to welcome Nate Chilton to the Tealinc team! Harnessing Tealinc’s legacy of providing unparalleled service to our clients, the addition of Nate will help us reach even greater heights with our clients, vendors, and rail industry colleagues. By leveraging Nate’s railcar industry expertise, financial and business acumen, and customer-centric philosophies, we are excited to significantly grow our railcar portfolio and enhance our railcar offerings, all while continuing to exceed client expectations!” commented Julie Mink, President – Tealinc LLC.
Nate holds an MBA from the University of Chicago Booth School of Business and an MS in Mechanical Engineering from the University of Illinois at Chicago. Nate is an avid outdoorsman and in his spare time can be found traveling, hiking, camping, or otherwise exploring Colorado with his wife and young son.
As we embark on this new chapter, we invite our clients, partners, and vendors to connect with Nate and explore railcar solutions (lease, sell, buy) that meet your unique needs!
Contact Nate Chilton Today:
Nate Chilton
Director: Railcar Leasing & Sales
(815) 762-0184
nate@tealinc.com
www.tealinc.com
Tealinc LLC – Moving Forward with Excellence!
Tealinc LLC (“Tealinc”) is a customer-centric freight railcar owner, lessor, and rail transportation solutions company. Tealinc partners with novice and experienced rail shippers in nearly every industry supported by rail and provides solutions through its three core competencies including 1) leasing, purchasing, and selling nearly every type of freight railcar, 2) providing rail transportation management services, and 3) providing rail transportation consulting services. Tealinc has a geographic reach inclusive of all North America with focus on shippers on all US, Canadian and Mexican railroads. Additionally, Tealinc has an international presence having sold rail equipment to Peru and China.
Tealinc Announces Acquisition by Private, Family-Owned Firm
FOR IMMEDIATE RELEASE
Date: November 20, 2023
Tealinc Announces Acquisition by Private, Family-Owned Firm
Tealinc LLC, a provider of railcar equipment leasing, sales, and fleet management solutions, is excited to announce its acquisition by a private, family-owned premium finance firm. While the transaction details remain confidential, this marks a pivotal new chapter in the company’s growth and long-term strategy.
With the new ownership structure, Tealinc gains access to increased capital and expanded operational capacity—positioning the company to acquire railcars in larger volumes and deliver faster, more competitive service to its customers across the rail industry.
Julie Mink, President of Tealinc, shared, “This acquisition provides a springboard for expanded services and fleet capabilities. Backed by a team with over 115 years of combined rail experience and now strengthened by additional resources, we’re laser-focused on delivering greater flexibility and innovation to the shippers and customers we serve.”
New Chapter, Same Core Values
While ownership has changed, Tealinc remains rooted in its commitment to exceptional service and industry integrity. The leadership team—CEO Darell Luther, President Julie Mink, and Directors Shannon Rodgers and Yvonne Lufborough—continues to drive the company forward with the same passion and rail expertise that Tealinc customers have trusted for over two decades.
Looking ahead, Tealinc will focus on fleet expansion, strategic acquisitions, and deepening its collaborative footprint across the rail industry.
About Tealinc LLC
Founded by Darell Luther in 2002, Tealinc LLC specializes in railcar leasing, sales, and rail fleet management solutions. The company serves clients across industries including agriculture, energy, manufacturing, recycling, and more. Tealinc is known for delivering tailored solutions that help customers optimize their rail transportation assets.
Tealinc LLC – Moving Forward with Excellence!
For further information, please contact:
Julie Mink, President
Tealinc LLC | www.tealinc.com | julie@tealinc.com
Office: (720) 733-9922 | Mobile: (720) 384-6385
Empty Railcar Freight - Exploring A Different Approach (Published by Freight Tracks in the UK, February, 2022)
Tealinc LLC – CEO, Darell Luther, article published in the February 28, 2022 issue of Freight Tracks. Follow the link or read through the image here.
Tealinc Authors "Emerging From the Supply Chain ‘Hell Tour’" (Published by Railway Age, February 2022)
Published February 7, 2022
Link: https://www.railwayage.com/analytics/emerging-from-the-supply-chain-hell-tour/
Link: https://sites.psu.edu/jlw6607/2022/02/09/eportfolio-article-1/
Emerging From the Supply Chain ‘Hell Tour’
Years before Guns N’ Roses released “Welcome to the Jungle,” they set off on an adventure along the West Coast toward Seattle that would later become known as “The Hell Tour.” Their elected mode of transportation, a 1977 Oldsmobile with a U-Haul trailer, broke down and sent them hitchhiking for 40-plus hours, carrying only their guitars. They missed several shows and played on borrowed amps when they finally arrived.
Does this remind you of the 2020-2022 global supply chain? What started in 2009 as a steady growth streak for worldwide transportation demand was reigned in and hit hard with the COVID-19 outbreak in early February 2020. Since then, the global supply chain has undoubtedly been on its own “Hell Tour.”
In second-half 2021, all indications were that the world was working its way out of this Hell Tour and getting on track for record growth in just about all sectors (33.1% in 3Q2021 based on the Federal Reserve). The growth was and continues to be explosive in the United States, so much so that supply of goods and the method of moving that supply (from ship to truck to rail to barge) continues to be a real challenge and looks to be for the foreseeable future.
While our focus in this article is centered on rail as one part of the shipping artery, it cannot go unrecognized that the problem with delayed imported goods starts at the ports. U.S. imports have faced delays for weeks/months, not days, and at costs that are exorbitant on anyone’s budget. At any given time, there have been 30 to 60 plus ships in the Long Beach and Los Angeles port system trying to unload containers. For the return trip, the focus remains on trying to reload the ships with empty containers going back to Asia to be refilled. East Coast ports are faring a little better, but not markedly so, and bulk commodity berthings are stuck in the quagmire. As for exports, rail traffic from and to those ports is causing an export resource drain for the many products the U.S. ships oversees.
One of the hardest hit industries has been agriculture. Many of the containers that would be rerouted to agricultural loading locations are being sent back to ports empty because the controllers of the containers don’t want any further delays in getting their containers back to the export port. Because the U.S. exports approximately 25% of the grain shipments it produces in container or via bulk ships, container shipping companies make significantly more money bringing goods to the U.S. than from the U.S.
Other industries feeling the pain include scrap metal shippers, mineral shippers, fertilizer shippers, coal mines and general bulk commodity shippers that require a bulk ship vs. a container ship.
The result is a not only an export stagnation, but also an overflowing reduction of domestic traffic being handled. These two separate and distinct markets get in the way of each other, causing further bottlenecks in the rail system. The cause of the delays are repetitive with the now-old news. Shippers are having difficulty in transporting products with pent-up or increased demand due to a COVID-19-induced manpower shortage, unwillingness of labor wanting to come back to work, and skilled labor not being readily available to bring back from furlough. While news is made in the more dramatic sectors (it’s hard to ignore when 90 container vessels are waiting to unload when the normal backup is one or two), there are more delays occurring in the domestic business than is accounted for.
When we look at what’s powering the nation, there have been and continue to be coal-fired utility plants running short of coal for steam generated electricity. In some cases, these companies were as high as 50% behind their planned coal take. That causes true reason for alarm in an industry that is working hard to upgrade its infrastructure and go green while still supplying energy to the existing grid. Meanwhile, aggregate, sand and gravel shippers, which generally operate in closed loop systems, are seeing delays of 25% on dedicated trains and 15% delays on the manifest side. Grain shippers are paying $100-$200 over railroad railcar auction sites and the secondary market to get railcars and trains booked to address bulk shipments to domestic markets. Scrap metal shippers running to U.S. steel mills are having a price differential upwards of $300 per railcar simply to show up with a load of scrap ready to be processed. We’re certain the list of commodity-specific delays is significantly longer, but you get the message. Overall, it continues to be a Hell Tour.
Meanwhile, what about the railroads? No one hates a delayed railcar more than a railroad. The same series of events that caused the pandemic-induced shortages for the shipping community are the same ones that are causing delays in the rail industry. The herky-jerky attempt to bring a sense of normalcy to these resource demand imbalances are requiring shippers to take a new look at their logistics.
What’s the New Transportation Look?
America is resilient, and we’re all in the process of working our way through these challenges. The intertwining of truck, barge and rail freight with ocean freight is uncanny. What are some of the action items being taken?
In late 2021, Walmart, Home Depot, Cosco, Dollar Tree and many others started chartering ocean going vessels to exclusively transport their products. These retailers want to control a bigger part of their destiny. If you’d been to most any retail store during 2021, you could certainly tell their shelf space wasn’t being fully utilized. Most certainly, there are bulk shippers considering their own vessel charters or ownership that didn’t ever think it would be on their radar screen.
Manufacturers are diversifying sources for critical materials and components. This might include geographic diversion with the same or alternative suppliers. It’s a small wave now, but a prolonged pandemic will continue to push manufacturers to consider “near-shoring,” bringing back manufacturing to North America. At times like these, the cost of not having product readily available far outweighs the labor savings found in the Far East.
Reconsideration of inventory levels is another focus. Raw materials may very well be the lowest cost of the entire process. Just-In-Time inventory approaches are getting a new look. Is JIT inventory, supported by a long physical distance subject to many supply chain disruptions, a better investment than simply having more widgets on hand?
Is This Cost of Doing Business Worth It?
We are a railcar lessor, rail fleet manager and rail transportation solutions provider, so we have a lot of first-hand logistics, supply chain and specifically railroading experience. Our clients remind us frequently that the values of having and not having railcars available to timely ship product ranges from $45 to more than $250 per railcar. This is over and above any railcar rental or maintenance costs. This theme seems to be repetitive across many commodities. What value do you place on having a railcar available to load or not?
Our Advice
Examine logistics bottlenecks and consider alternative plans. The ocean-going industry is hogging the limelight with ships sitting at sea waiting to unload. It’s easy to count the delays and impact with ships. Rail transportation bottlenecks are as relevant but aren’t as transparent. The rail bottlenecks cut across all commodities, and this diversification makes those slowdowns, misroutes and lack of railcar supply less noticeable.
Loaded railcars get quite a bit of attention, so a simple daily review can tell you where your loads are. What becomes significantly more important is the question of “where are my empty railcars for the next load?” Private railcars have grown to comprise almost 80% of the total railcar interchange fleet in North America. The slack in the rail system must be in the private railcar arena. Railroads have such massive investments in track and infrastructure they’ve strategically chosen not to be a primary railcar provider.

As a shipper or receiver, it’s up to you to put slack in the rail transportation system by having your own railcars, plenty of track space to accommodate what you’re going to load or unload on a daily basis, and a location, possibly off-site, where you can store a backup of railcars to fill in for supply chain disruptions. It’s the cost of doing business in the new era.
Darell Luther is CEO and Founder of Tealinc Rail Transportation Solutions.
Why Inspecting Rail Equipment is Not Just for Railroads: "Boots on the Ground" - By Darell Luther Published in the January 2021 Waste Advantage Magazine
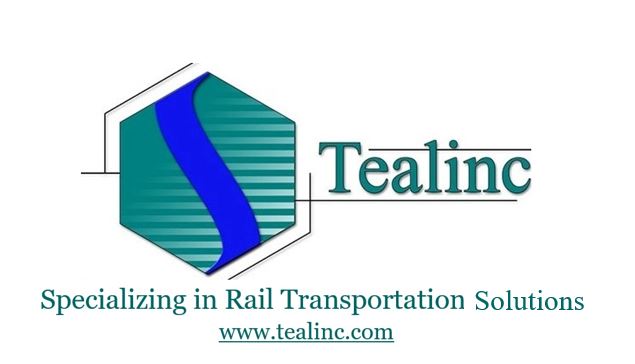
Darell Luther, Tealinc’s Founder & CEO Contributes Another Article to Waste Advantage (view the January 2021 Waste Advantage Magazine edition)
Why Inspecting Rail Equipment is Not Just for Railroads: “Boots on the Ground”
Railroads are ever pushing the envelope on asset use. It is partially up to you as a railcar lessee, rail shipper and railcar user to fill in the gap to ensure your shipments get transported in a safe and mechanically sound railcar.
-Darell Luther
Rail equipment is mechanical by design. A good mechanic will tell you anything mechanical is a just a repair waiting to happen. The constant wear from being transported around the country in different climatic conditions, different handling modes and different loading and unloading situations does cause wear on railcars. Running repair items such as wheels, brake shoes, air hoses, couplers, draft system, car cushioning units, etc. all wear out over time and use and even quicker under abusive conditions. Abusive conditions occur more often than you think. When tracking the movement of a railcar across the country from northern minus 20-degree dry winter days to southern 70-degree muggy winter temperatures are all causes of mechanical impediments. Inundations of rain, snow, saltwater, ice and heat will all cause mechanical problems over time.
In the quest to go faster, farther and cheaper the rail transport industry is trending towards skipping an important component of providing a safe and efficient supply chain. That is the railcar inspection process conducted on the ground. While hopeful electronic gadgetry will do some of the work, e.g. Kips wheel impact load detectors (WILD), truck hunting detectors (THD) and other component wear detectors in testing or in process of being developed, there is not a substitute for boots on the ground inspections.
“Boots on the Ground”
We have seen two significant cases where one party thought the other was doing the inspections and neither was doing them. In this case, the company that actually leased the railcars did not have any idea of what was or was not being done because their lease was a full-service lease. The pending result was the potential bad order of an entire unit train which was narrowly avoided. In this case saving significant product cost delays built into the company sales contract. In another case we caught the indiscretion because we proactively manage the fleet. It could have resulted in a significant number of railcars being bad ordered while in route causing a costly supply chain disruption for the shipper.
Following is some “boots on the ground” guidance from the folks at the Association of American Railroad (AAR) and others in the industry that have a regular inspection routine.
Item | Description |
Car Body | Inspect the car body for broken, damaged or missing hand holds, sill steps, cross over platforms, roof damage and corrosion, roof platforms, holes in the body that would leak product. Close and secure doors on boxcars, close and secure hatch covers, close gates and inspect door pans for damage. Inspect top chords, side stakes and side sills for damage. Inspect flat cars for appropriate camber. |
Wheels & Bearings | Inspect wheels for obvious slid marks, spauling or shelling, high flange or thin flange. Inspect bearings to insure they don’t spin on the axle and aren’t leaking grease. Once a quarter run EHMS for the cars to ensure compliance with KIPS results. |
Brake Mechanism | Inspect the brake shoes for wear. If excessively worn, roughly ½” tread remaining, replace with 2” high frictions shoes. Inspect hand brake and brake levers for general operation. Inspect brake hoses for wear and compliance with hose dates. Once a quarter run the EHMS for the cars to ensure compliance with air brake test date requirements. |
Trucks | Check the truck spring group for broken or missing springs. Railcars that have snubbers need to be inspected for leakage. Observe truck shoe height to gage truck shoe height compliance. Inspect truck side bearings – roller and constant contact – for excessive wear. |
Couplers, Yoke and Draft | A quick inspection of the coupler for bypass situations, broken, bent, missing or general wear will suffice. Also look for evidence of excessive force in coupling by inspecting the striking plate for evidence of damage. Be sure the draft key is in place and the yoke doesn’t show evidence of cracking. |
While it is not necessary to be as thorough as we have outlined every time a railcar rolls in to be loaded, it would pay dividends to get this involved at least once a quarter. Modified inspections should at least cover safety items such as brake shoes, hand holds, cross over platforms and hand brake wheel operations.
Waste and Scrap Transportation
As a member of the waste industry you should be seeing some recovery of rail shipments. According to the Associations of American Railroads the waste and nonferrous scrap business has been trending up over the past 30 weeks topping out in November 2020 at around 4,200 originated rail carloads per week. That means more railcars and trains hauling waste and nonferrous scrap. This uptick in business may catch some shippers unawares of the mechanical requirements of their rail fleets. Do not be lulled into complacency, inspect those railcars.
Railroads are ever pushing the envelope on asset use. It is partially up to you as a railcar lessee, rail shipper and railcar user to fill in the gap to ensure your shipments get transported in a safe and mechanically sound railcar.
Darell Luther is CEO and founder of Tealinc LLC (Forsyth, MT), specializing in rail transportation solutions and solving rail transportation challenges. Darell has also been President of DTE Rail and DTE Transportation Services Inc., President and co-founder of Fieldston Transportation Services LLC, President and founder of Focus Transportation Services, Managing Director of Coal and Unit Trains for the Southern Pacific Railroad, and has had Directors positions in marketing, fleet management and integrated network management at the Burlington Northern Railroad. Darell has nearly 32 years of rail, truck, barge and vessel transportation experience mostly concentrated in bulk commodity and containerized shipments. Darell’s vast comprehension of the logistics chain, phenomenal leadership skills, industry knowledge and ability to think creatively has propelled Tealinc’s dynamic success. He can be reached at (406) 347-5237 or via e-mail at darell@tealinc.com.
For more information about leasing or buying railcars or any other rail transportation related issue, call (708) 854-6307 or e-mail webmail@tealinc.com.
Darell Luther Featured as Columnist In National Publication for Showcasing his "Waste-By-Rail" Knowledge
FOR IMMEDIATE RELEASE…
Contact: Darell Luther
Phone Number: (406) 347-5237
Email: Darell@tealinc.com
Tealinc LLC CEO Featured as Columnists in National Publication
Darell Luther showcase rail expertise as contributor and columnist to leading industry magazine
Forsyth, MT– Tealinc LLC CEO Darell Luther has been featured as a columnist within the popular industry magazine Waste Advantage with a monthly column featured under the title of “Waste-by-Rail”. Mr. Luther’s articles showcase his extensive rail knowledge and expertise and highlight the application within the waste industry. While the articles focus on issues related to rail transportation within the waste industry, readers will find the material applicable to varying additional industries.
We invite you to read the monthly articles by clicking the links below.
2017 Articles:
- March 2017: Second of Two Parts: Railroad “Think”: Understanding Logistics
- February 2017: First of Two Parts: The Value in Rail Transportation Logistics
Click here to read 2014 Waste Advantage Archives
Click here to read 2013 Waste Advantage Archives
Click here to read 2012 Waste Advantage Archives
Darell Luther is Founder and CEO of Forsyth, MT-based Tealinc LLC, a rail transportation solutions and railcar leasing company. Darell’s career includes positions as president of Tealinc LLC, President of DTE Rail and DTE Transportation Services Inc., Fieldston Transportation Services LLC, managing director of coal and unit trains for Southern Pacific Railroad and director’s positions in marketing, fleet management and integrated network management at Burlington Northern Railroad. Darell has more than 24 years of rail, truck, barge and vessel transportation experience concentrated in bulk commodity and containerized shipments. Darell can be reached at (406) 347-5237, via e-mail at darell@tealinc.com or visit www.tealinc.com.
Tealinc Ad “Featured Product” in Pit & Quarry Magazine
Here at Tealinc LLC, we are honored to provide rail transportation solutions to various industries moving today’s freight. Our recent ad highlighting our 2300 Cube Open Top Hoppers was listed as a Featured Product and was showcased as the Equipment of The Day within the popular online version of the Pit & Quarry Magazine on August 9, 2012.
See Tealinc LLC in Aggregates Manager Magazine
Tealinc LLC is proud to be featured within the leading industry magazine Aggregates Manager. The ad showcases Tealinc LLC services, industry expertise and knowledge and provides direct contact information.